Prototyping Process
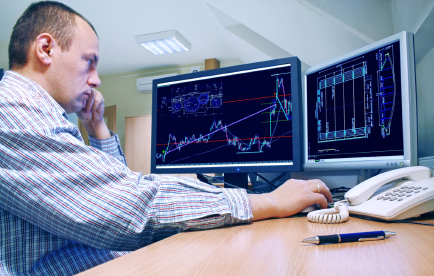
Successful prototyping requires a systematic process with specific deliverables and reviews at each development phase; this enables continuous judgment and open decision making on product scope, risk, schedule and budget.
The following is the description of an ideal phased prototyping process:
- Phase 0: Concept and Feasibility
- Phase 1: Design, Prototype Engineering, Assembly and Test
- Phase 2: Engineering-controlled Production of Advanced Prototypes for Field Testing
- Phase 3: Preproduction and Manufacturing
- Phase 4: Sustaining Engineering
Phase 0: Concept and Feasibility
In this initial phase, engineers should review the project requirements, develop a comprehensive plan of action, and integrate all key parties into the development: the Client, designers, engineers and supply chain specialists. A specialist should run an investigation of alternative product concepts and associated manufacturing methods, followed by an evaluation of these using simulations and physical models. Developing conceptual, mechanical and electrical layouts to identify risk areas and generate a preliminary estimated BOM (bill of material) allows experts to determine overall feasibility. At the conclusion of Phase 0, The models and concepts are discussed in order to select a concept based on the feasibility and risk findings. This phase is concluded with revised estimates and a project plan for subsequent stages.
Phase 1: Design, Prototype Engineering, Assembly and Test
During Phase 1, The design and analysis are completed, prototype-level documentation is generated and materials are procured. Finally a alpha prototype units are constructed for internal testing to validate function and performance according to an agreed-upon test plan. At the conclusion of Phase 1, a comprehensive review of the prototype design and test results should be produced.
Phase 2: Engineering-controlled Production of Advanced Prototypes for Field Testing
During Phase 2, final design and documentation adjustments are completed based on test results in Phase 1. Advanced prototypes are built by skilled engineering technicians. Extensive field-application trials are conducted jointly between engineers and the product owner. If any issues arise during this testing, additional design changes and associated documentation updates are made. At the conclusion of Phase 2, a comprehensive review is conducted and a production ready documentation package for manufacture should be prepared.
Phase 3: Preproduction and Manufacturing
Phase 3 consists of customizing the manufacturing process and allows for the scaling up of product capacity. Continual assessment, quantification and reports of Supply Chain effectiveness are crucial.
Phase 4: Sustaining Engineering
During Phase 4, although thorough due diligence in phases 1 and 2 will reduce the chance, the customer may need ongoing engineer support due to various reasons in phases 3 and 4:
(1) the product may need some modifications after actual use by a wide range of customers under diverse operating conditions that may not have been covered during field testing, (2) accelerated life tests may not have identified all the issues that could arise from wear and tear over time, (3) continuous improvements for better performance and lower cost, (4) component obsolescence during the product life cycle requires identification and evaluation of replacements that may not be drop-in and require some level of design change.